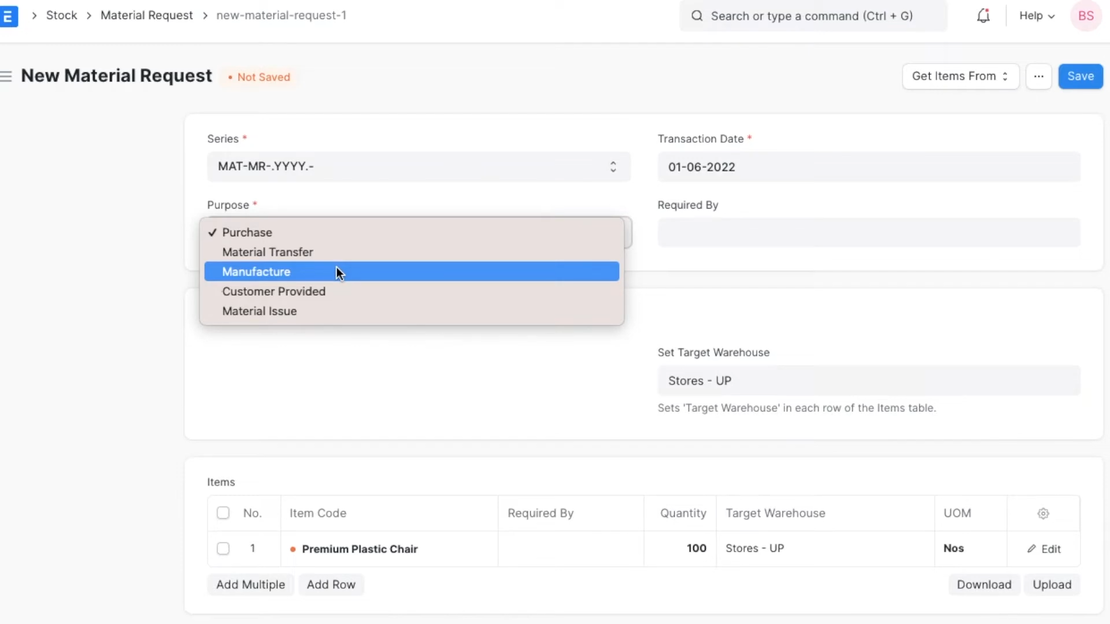
Buying Module in ERPNext
Table of Contents
Procurement Management System:
I am working on a project which is for procurement and some time ago I had used ERPNext for exploration. It occured to me that ERPNext can be used instead of creating own project.
Frappe school’s Procurement course link.
Course material:
Regardless of industry, procurement of raw materials and other goods and services is extremely important and is often one of the primary activity in any organisations. Procurement management not only keeps business running smoothly but also can help save time and money. It makes sure any production processes and the general working of an organisation is not compromised because of lack of resources.
The Buying Module in ERPNext competently covers the entire process of purchasing and helps users document, calculate and make the best decision based on the resources at their disposal. The module covers everything from Suppliers and Supplier Quotations to Material Requests and Purchase Orders and ensures that every step is completed methodically.
This course is appropriate for anybody who is in charge of any procurement process. This course runs over six chapters and covers basic but detailed concepts that are a part of the procurement and buying methods in an organization.
This course consists of following chapters
Table of Contents
- Supplier Master Data Management
- Material Requests
- Supplier Quotations
- Purchase Orders
- Supplier Scorecards
- Reports
Supplier Master Data Management
This module is all about Suppliers, as these are vendors from which the orgnization will take thier products or services.
Here we have added Supplier in system.
Details:
- Address
- Account
- PAN, GST details.
- Currency
- Contact details.
Grouping of supplier.
Supplier scorecard helps to grade the supplier for better supplier selection.
Material Requests
A material request is an internal document that contains details about any products or services required in an organisation. They are created for various needs, for example, if raw materials are needed for production, or if stationary is required for internal use in the organisation or even for assets like laptops.
These material requests contain information and relevant details for these requirements, including reasons and are usually fulfilled by the procurement department of an organisation.
Setting a process within the organisation for requesting products or services will help streamline communication channels between the departments requesting materials and the procurement department.
As an organisation, it is also necessary to ensure that approvals are enforced for each material request; this will assure that only authorised and needed items are procured and processed through pre-defined workflows.
Whatever products / materials / services are required in an organization we will create a Material request.
From Material request we can create:
- Purchase Order: Order placed with a supplier with given items.
- Request for Quotation: A document sent to suppliers asking them for rates of products.
- Supplier Quotation: Document provided by the supplier.
Supplier Quotations
Contacting multiple suppliers and requesting their quotes is important to find the best products at the right price. As an organisation, when you need to purchase certain goods or services, you won’t just contact a single supplier and buy goods from them, you will need to contact multiple potential suppliers and collect relevant information from them.
In response to this request for quotation, potential suppliers will share documents of information that are known as Supplier Quotations. These quotations will contain prices, product specifications, and terms and conditions. Comparing different quotations from different suppliers will help ensure that you get the best deal.
If you’ve sent out a lot of requests for quotations and received a large number of responses in return, you can even automate this process using the Supplier Portal in ERPNext. Once you select a supplier, you can issue a purchase order for them.
1. Request for Quoatation.
After creating RFQ we can send as mail.
2. Configure Supplier Panel.
We can also invite supplier as user into ERPNext.
After loging into the our system supplier will see:
They can open any RFQ and submit their details:
3. Supplier Quotation.
If there are Supplier quoatation sent out of ERP system, it can be added:
4. Comparing Supplier Quotations.
Multiple supplier quotations can be compared:
Purchase Orders
A purchase order is a binding contract between you, as an organization, and your supplier stating that you will buy a certain number of products or services from them under set conditions.
A purchase order is an important part of any defined procurement process and ensures that you obtain products or services from the right suppliers at the right price and quality. A purchase order serves more than one purpose. Not only does it act as a document that records and informs suppliers about what is needed when, but it also allows internal stakeholders to know what is expected from any particular supplier.
A Blanket Order is an order from a customer to procure products or services for specific items over a period of time at pre-negotiated rates. Blanket orders can also be used to procure products or services from a supplier over a period of time. A delivery schedule is also shared along with the blanket order.
After comparing all the quotes from suppliers/vendors a purchase order is created.
Purchase order is created against items, those items can be take from Supplier quotation.
After creating PO multiple documents can be created:
- Purchase Receipt
- When received listed items from supplier
- Purchase Invoice
- A bill created against this PO
- Payment request
- A Request for payment to made against this PO
- Payment
- Which indicates that a payment has been made against this PO
- Subscription
- On repeat based on customised frequency
Supplier Scorecards
Most companies, especially those involved in manufacturing, have multiple suppliers for their products and services. When procurement processes take place at a large scale, purchase managers need to pick suppliers based on numerous criteria, including cost, quality, time and more.
A supplier scorecard is an evaluation tool in ERPNext that helps assess the performance of suppliers that work with an organisation. They can be used to keep track of the quality of items delivered, delivery, and responsiveness of suppliers across long periods. It calculates a score for each supplier based on this data and helps purchase managers make calculated decisions about which suppliers to work with.
Automating the complex process of calculating the effectiveness of each supplier based on multiple customised factors can prove to be immensely valuable and make the Supplier Scorecard in ERPNext a robust support system for decision-makers.
Score variables
Scoring Criteria
Reports
Procurement of materials, goods and services is a large part of any organisation. Procurement managers are responsible for buying the right quantities at the right time since these decisions can considerably affect the company’s cash flow and profitability.
Suppliers are as crucial as customers are, and procurement managers must provide them with accurate information about needed materials, delivery dates etc. Procurement managers also need to diligently track open material requests, anticipate demands in goods and even account for disruptions in the organisation’s supply chain.
Having a dedicated Reports section for managers to view and keep track of analytics helps streamline data-driven decision-making processes.
Add Supplier
Create Material Request
Send RFQ, Request For Quotation
Recieve Supplier quotations
Compare and select a perfect quotation.
Create Purchase order
Payment